自社業務運用にフィット!現場起点で販売管理業務を最適化する方法とは?
製造業におけるクラウド型販売管理システムの導入事例
公開日: 2023.12.01
HCSNewsLetter 第230号
取材協力
専務取締役 小西 春輔 様
販売管理G リーダー 河原 晴美 様
販売管理G 橋本 祐子 様
経営管理G 藤田 葉月 様
タカノクリエイト株式会社様について
[所在地]
石川県加賀市宇谷町タ1番地5
[事業概要]
回転寿司皿、業務用食器・備品、プラ箸、オリジナルキャラクター食器などの製造販売
3つのシステムにまたがっていた販売管理業務を、『ターコイズ販売管理 V5 クラウド』導入により業務最適化し、よりスピーディーな現場判断、より正確な経営判断が可能になった事例をご紹介いたします。
- 課題
- (1)販売管理・工程管理業務の最適化
(2)情報の一元化・見える化
(3)製造原価や在庫評価額の正確な管理
- 効果
- (1)重複業務の削減で担当者数は3/4に
(2)個人から組織管理になり属人化解消へ
(3)より正確な財務状況の把握が可能に
目次
販売管理業務の最適化を実現するための「3つの課題」
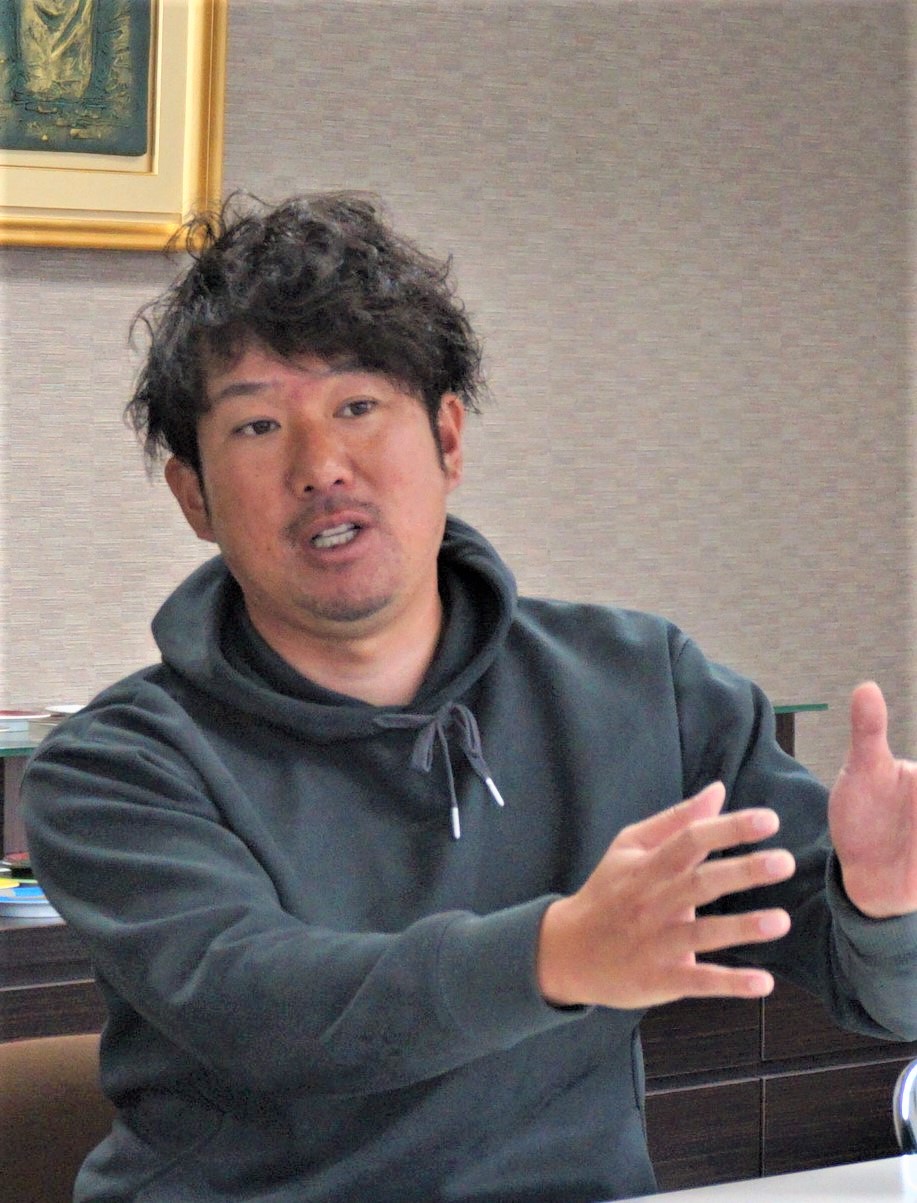
専務取締役 小西 春輔 様
-検討のきっかけを教えてください-
3つのシステムを利用していたのですが、システム間でデータの自動連携ができませんでした。そのため、データの二重入力や分散登録など、非効率な業務が数多く発生していました。当社の業容が拡大する一方で、業務の在り方に疑問を持った現場が「このままではいけない」と問題提起したのがきっかけですね。
-3つのシステムを利用することになった経緯を教えてください-
当社の前身である株式会社タカノは、山中漆器の素地を製造し、塗職人に卸売していました。手書き伝票の運用をシステム化する目的で、今から20年以上前に販売管理システムを導入。
その後、全国でも有名な回転すしチェーン店各社のすし皿製造・販売を業容とする当社が創立、タカノと同じ販売管理システムを導入。タカノはすし皿の素地を製造するようになり、当社がタカノから素地を仕入れ、塗装して販売する体制に。そして、すし皿製造・販売の業容拡大に伴い、当社がタカノの業容を吸収しました。ところが「タカノ」と「当社」の「販売管理システム」は統合することなく、使い分ける運用のままに。
そして、当時の販売管理システムにはなかった工程単価管理ができるよう「工程管理システム」を導入したのです。
-どのような課題をお持ちでしたか?-
課題1:販売管理・工程管理業務の最適化
3つのシステムを併用していたので、ムダな作業が多く、事務や現場担当は大変な思いをしていました。
「1つ目」の販売管理システムでは素地の原材料や成型品を管理。「2つ目」の販売管理システムでは塗装以降の工程の半製品および完成品を管理。「3つ目」のシステムでは工程管理を行っており、一元管理されていなかったため、各システムに同じ情報を入力する手間が発生していました。コード体系もシステムごとに異なるため、データを紐づけることもできず、非常に管理しづらいものでしたね。
課題2:情報の一元化・見える化
システム間が連携していなかったので、それを補う形でExcelを活用していました。社内ルールが明確ではなく、Excelを各自で管理していたので、情報共有に課題がありましたね。
例えば、作業指示。各担当者がExcelのひな形を持っていて、様式は各自バラバラ。必要事項を入力し、印刷後に手書きで指示を追記することもありました。各自が管理しているので、他の人からしてみたら、どこを見れば情報を確認できるのかわかりませんでした。
納品書受領から仕入計上までに数日かかることも課題でしたね。
製造工程の一部を外注することもあり、外注先から受け取った納品書(原紙)を最初に社内の各現場へ回覧します。仕入計上のために事務所に戻ってくる頃には、納品書受領から3日ほど経っていることも。実際は入荷して在庫があるはずなのに、仕入計上の遅延で実態とズレが生じ、誤った判断をしてしまうリスクがありました。
課題3:製造原価や在庫評価額の正確な管理
併用していた2つの販売管理システムを製造工程に応じて使い分ける運用だったため、工程ごとの製造原価を正確に把握することができませんでした。
また、内製と外注、さらには外注先ごとに工程単価が異なるのですが、システムで複数単価を管理することができず、便宜的に全体の平均単価を工程単価として設定するしかありませんでした。ところが、外注先の職人たちが高齢化により引退したことで、内製比率を上げた結果、便宜的な工程単価と実態の乖離が大きくなってしまいました。
自社の財務状況を正しく把握するには、製造原価や在庫評価額の正確な管理は不可欠ですが、内製と外注の工程単価を分けて管理することは大前提。外注先ごとの工程単価管理までこだわりたいと考えていました。
「3つの課題」を解決する「ターコイズ販売管理 V5 クラウド」
-採用の決め手を教えてください-
HCSさんから「カスタマイズでの対応が可能」とのご説明いただいたことが決め手です。
当社は業務が複雑で、工程も多くあり、いろんな人がかかわるので、システムを業務に合わせるというコンセプトで検討していました。だから「HCSさんしかない」と思いましたね。
実は、他社さんにも相談していて、話がずいぶん進んでいた状況。システムとしての完成度はHCSさん以上と感じていました。ただ、他社さんのご提案は、システムに当社の業務を合わせるものでした。業務ごとにどの機能を使えばよいか、システム利用方法の答えは明確でしたが、今まで通りに業務が回るイメージができませんでした。
その点、HCSさんは私たち以上に当社の業務を理解してくれた上で、業務に合わせた解決策を示してくださいました。検討を進める上でのサポート体制がすごくよかったですよ。
-工夫された点を教えてください-
システムの検討を始める前に、STEP0として業務プロセスの改善から取り組みました。システム化の準備段階です。業務棚卸に半年以上かけました。ただ、3つのシステムを利用していたこともあって、システム化のイメージはできていましたよ。管理が必要な項目や必要な業務、重複している業務、紙運用などあえてアナログのまま残す業務が棚卸できました。
また、業務プロセス改善は現場主導で進めてもらうことを意識しました。現場から出てくる意見で作り上げると、いつの間にか当事者意識になる、そう考え、課題の洗い出しから始まり、各グループで毎週打ち合わせを実施。あるグループは最初「自分たちはシステムと関係ない」という感じでしたが、だんだん関わってくれるようになっていきました。
併用していた2つの販売管理システムでは、同じ商品でも異なるコードで管理していたので、共通化するのは苦労しました。コード体系の見直しでは、製品名主導だったのをコード主導に変更、コードを見ればどの工程の製品なのか誰でもわかるようにしました。
製造指示書はA4サイズに収まる情報量になるよう、社内で協議してレイアウトを統一化しました。欄外に指示内容を手書きで補足していたくらいなので、どの項目を残すのかを決めるのには苦労しましたね。
導入効果・メリット
-取り組みの効果はいかがでしたか?-
効果1:重複業務の削減で担当者数は3/4に
3つのシステムを統合したことで、二重入力などの重複業務がなくなった実感があります。1箇所に入力すれば、仕入も立てられるし原価も計算されるので、たくさんの人が入力に関わる必要がなくなりました。その結果、以前はシステム登録担当が8名だったのが、6名で済むようになりました。
また、コード体系を見直したことで、同一製品でも工程ごとに別コードだった問題は解消され、全工程一気通貫で製品を管理できるようになりました。
効果2:個人から組織管理になり属人化解消へ
自分が知りたい情報を、システムのどこを見ればよいか分かるようになりました。それまでは個人で作業していて周りとのつながりが感じられませんでしたが、システム上で見えるようになったことで、周りの人の作業計画・実績まで理解できるようになりました。
各担当がExcelで作成・管理していた作業指示の内容もシステムに一元管理され、以前は紙やExcelなどいろんなものを確認しないといけなかったのが、1つのシステムを見れば確認できるようになったので、効率がよくなりました。
情報が一元管理され、情報を個人で管理していたものが組織で管理できるようになり、属人化解消の第一歩になったと思います。
効果3:より正確な財務状況の把握が可能に
工程が進むごとに在庫評価単価が積み上げられる仕組みにしました。さらに商品別工程別依頼先別に工程単価を設定できるように。内製と外注はもちろん、外注先により異なる単価を設定し、より厳密に在庫評価できるようになりました。
そのおかげで、工程単価を比較して、より安価な外注先を選定することができます。一方、単価よりも納期を優先しなければいけないケースでは、納期の条件を満たす外注先の中から適正単価を判断できるようになりました。
今後の展望
-今後、取り組みたいことをお聞かせください-
今回のシステム導入で製造原価や在庫評価額がリアルタイムに把握できるようになったので、財務の収益性を改善するために粗利の分析を、効率性を改善するために適正在庫の分析を行いたいです。
また新たな課題として、品質責任の所在を明確にし、製品品質を向上するためにトレーサビリティを確立し、品質異常時の対象ロットの特定・製造工程見直しなど、品質管理の体制を強化したいです。
さらに、適切な納期設定や繁閑のばらつきを平準化し、リードタイムの短縮を図るために作業負荷の実態を把握し、残業時間の最適化など労働時間問題にも取り組みたいです。
-インタビューにご協力いただきありがとうございました-
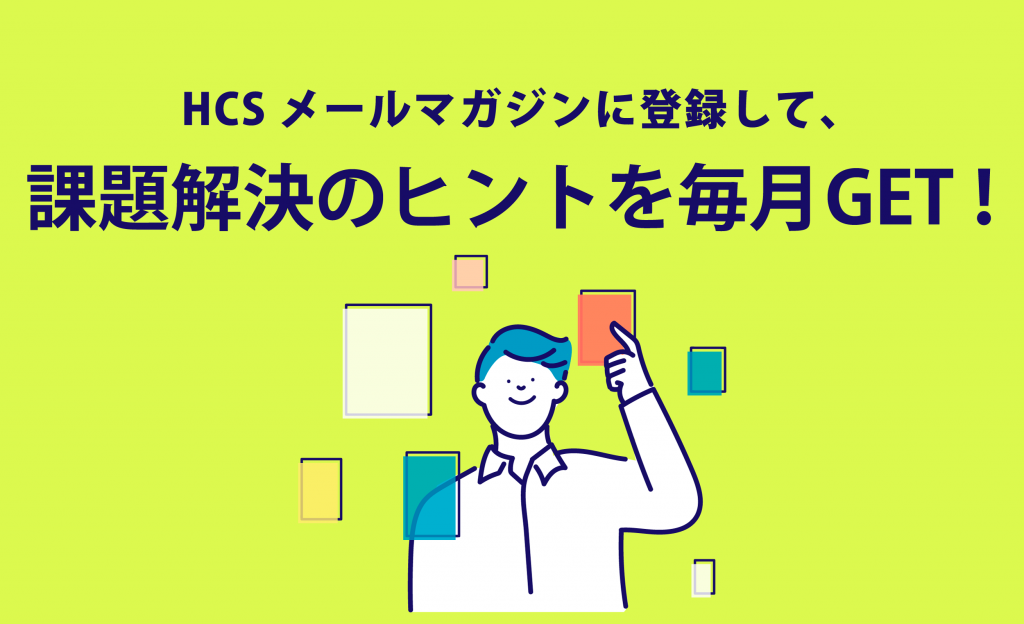
メルマガでお届け!北陸企業のIT活用事例から、課題解決のヒントが見つかる!!
(1)毎月、最新の事例をご紹介
(2)お客さまのIT活用成功事例を「事例集」として配信
(3)その他、コラムやイベント情報などをお知らせ
導入サービス
関連導入事例
経営戦略の立案を実現する販売管理のしくみとは?
- 導入サービス:ターコイズ販売管理システム
- 課題
- (1)クラウド活用によるBCP対策
(2)正確な販売実態の把握
(3)非効率な業務の改善
- 効果
- (1)属人化を解消、被災時も業務継続
(2)分析精度を向上し、注力業界を見直し
(3)毎月約3時間の売上集計作業がゼロに
数千パターンの加工品在庫をシンプルに管理する方法とは?
- 導入サービス:ターコイズ販売管理システム
- 課題
- (1)複数にわたるシステムと複雑な運用
(2)プリント品の複雑な在庫管理
(3)出荷指示作業に手間がかかる
- 効果
- (1)事業展開に合わせた統合システムに
(2)インストアコードで在庫管理の最適化に
(3)スムーズな在庫照会と出荷指示で作業効率化に
「一元化」と「見える化」による販売管理のデジタルシフト
- 導入サービス:基幹システム、TQダッシュボード
- 課題
- (1)Excelによる煩雑な資材管理を改善したい
(2)荷受検査の紙運用を見直したい
(3)市場別取引単価・数量を見える化したい
- 効果
- (1)資材管理を基幹システムに集約
(2)タブレットによるペーパーレス化
(3)市場への出荷数の最適化