倉庫内ピッキングとは?ピッキングの重要性、効率的に使うためのポイントを詳しく解説!
倉庫内ピッキングとは?ピッキングの重要性、効率的に使うためのポイントを詳しく解説!
公開日:2023.02.27
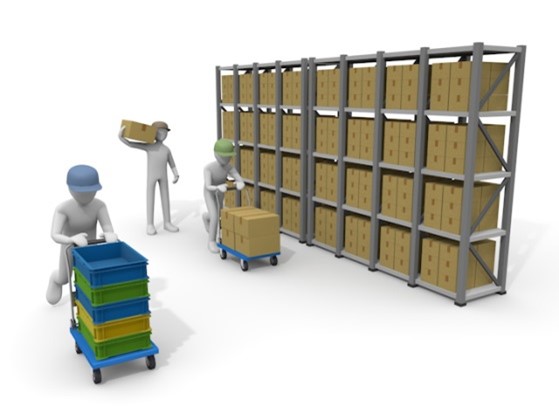
この記事では、伝票や指示書などを基に、商品・部品・材料など(以降「商品」と表現)を棚などの保管場所から取り出し、決められた場所へ集める「倉庫のピッキング」について取り上げます。
ピッキング作業自体は、比較的、単純な作業と考えられていて、「経験不問、短時間からでもOK」という条件でアルバイト募集も見かけることが多いです。
ピッキング作業は、製造業や小売・卸売業の業者が自らの物品を保管する「自家用倉庫」や、流通業・倉庫業の業者が他業者から物品を預かり保管する「営業倉庫」など、広い業種にわたって行われており、比較的単純な作業と考えられています。しかし、単純な作業だからこそ、作業のやり方や作業環境によって、その正確性や効率性・迅速性に、大きな違いとなって表れやすいです。
この記事では、トータル・ピッキングをはじめとして、ピッキングの方式や、その選択にあたり考慮する点、正確性・効率性などを上げる点について考えてみます。
1.ピッキングの重要性
オンライン・ショッピングで商品を購入した経験をお持ちの方も多いと思います。中には、リアル店舗を利用するよりも、オンライン・ショッピングの利用の方が多い方も、少なくないと思います。
その時に、価格だけでなく、いつ商品が届くかという時間も考えるのではないでしょうか?価格も機能も同じであれば、早く届く方を選ぶことが多いと思います。
先に述べたように、ピッキングは、製造業や小売・卸売業において、商品を出庫・出荷する時の一つの工程です。そのため、多くの商品を正確に、かつ効率的にピッキングする必要があり、その結果は、配送スケジュールへ影響を及ぼすだけでなく、製造業の場合は、生産ラインへ悪影響がでることにもなり兼ねません。
ピッキングは単調な作業ですが、正確性と効率性の両方が求められる極めて重要な作業です。
2.ピッキングの方式には、どんな方式があるか
ピッキングには4つの方式があります。それぞれの特徴とメリット、デメリットについて見てみましょう。
(1)トータル・ピッキング
複数の注文分の総量を、まとめてピッキングする方式です。先に複数の注文分の商品をまとめてピッキングし、梱包・発送の段階で、個別の注文に合わせて仕分けを行う方式です。畑に種を蒔く様子に近いことから「種まき方式」とも呼ばれます。
① トータル・ピッキングのメリット
複数の注文分をまとめてピッキングするので、作業者の移動距離・移動時間が短縮できることです。また、仕分け後、商品の残数が0であれば、正確に作業ができたと判断しやすくなります。
この方式は、出荷先が多いほど効果が高くなります。その中でも、商品の種類が多くなく、出荷量が多いと、一層、効果が高くなります。
②トータル・ピッキングのデメリット
ピッキング後、「仕分け作業」が必要であることです。仕分け作業のためには、仕分け用の作業場所も必要になり、また、仕分け作業をする人と時間がかかることです。
(2)シングル・ピッキング
個別の注文ごとに商品をピッキングする方式です。出荷指示書などの伝票を基に、倉庫内から指示書に書いてある商品を、都度集めて、梱包・発送する方式です。畑にある野菜を順に収穫する様子に近いことから「摘み取り方式」とも呼ばれます。
① シングル・ピッキングのメリット
伝票を基に、必要な商品を必要な数だけピッキング・検品・梱包・発送するシンプルな作業手順であるため、間違いが起きにくく、また出荷完了まので時間が短いことです。
②シングル・ピッキングのデメリット
作業者が、注文ごとに作業を進めるため、注文の数と同じ回数、倉庫内を移動するため、移動距離が長くなり総体の時間がかかることです。
(3)マルチ・ピッキング
シングル・ピッキングとトータル・ピッキングのいいところを合わせたような方式です。マルチオーダー・ピッキングという場合もあります。
仕分け・梱包用のダンボール箱などを、ピッキングカートに載せ、複数の注文分をまとめてピッキングしながら、同時に、ダンボール箱などに仕分けを行う方式です。
①マルチ・ピッキングのメリット
複数の注文分をまとめて、1回の倉庫内移動で、ピッキングと仕分け作業まで行うため、移動の距離と時間を短くできることです。また、仕分け作業を同時に行うため、作業を効率化できます。
②マルチ・ピッキングのデメリット
「ピッキング」と「仕分け」という作業を同時に行うので、ダンボール箱への仕分けを間違えるなどの間違いを起こし誤出荷につながるリスクがあることです。
(4)オーダー・ピッキング
オーダー・ピッキングは、シングル・ピッキングの別名として扱われることが多いです。
ただし、厳密に分けて考える場合もあります。この場合、オーダー・ピッキングはシングル・ピッキングで説明したとおり、個別の注文ごとにピッキングする方式です。シングル・ピッキングは個別の注文について、発送先を一単位としてピッキング作業を行う方式です。
シングル・ピッキング、トータル・ピッキング、マルチ・ピッキングの流れを図示してみます。
・シングル:注文ごとにピッキング後、そのまま梱包し発送
・トータル:複数注文分をまとめてピッキング後、注文ごとに仕分け後、梱包し発送
・マルチ :複数注文分を、注文件数分カゴを用意し、カゴに仕分けしながらピッキング後、それぞれ梱包し発送
方式 | 注文 | カゴ | 仕分け | 梱包 | 発送 |
---|---|---|---|---|---|
シングル | ![]() |
![]() |
![]() |
![]() |
![]() |
トータル | ![]() |
![]() |
![]() |
![]() |
![]() |
マルチ | ![]() |
![]() |
![]() |
![]() |
![]() |
3.どのピッキング方式を選ぶのがよいか
では、これまで考えてきたピッキング方式のうち、どの方式を選ぶと効果が高くなるでしょうか?それを考えるポイントに、「倉庫内での作業員の作業効率」、「出荷件数」、「出荷先数」、「SKU(※1)数」があります。
①トータル・ピッキング
「倉庫内での作業員の作業効率」を上げる点が最大のメリットであるため、移動距離・時間を削減できやすい、出荷件数が多く、SKU(※1)数が少ない場合に適しています。
店舗配送など、出荷先が少ないもしくは一定で、扱う商品の種類が多くなく、大量出荷の運用に適しています。
② シングル・ピッキング
注文の数だけ倉庫内を移動するため、出荷件数が少なく、SKU数が多い場合に適しています。
EC・通販などのBtoC系の物流センターなどに適しています。出荷先が多く、扱う商品の種類が多く、少量出荷の運用に適しています。
③マルチ・ピッキング
トータル・ピッキングと同様、「倉庫内での作業員の作業効率」を上げる点がメリットであるため、倉庫が広く、出荷オーダー数・件数が多い場合に適しています。
ただし、先に述べたように箱の入れ間違いが起こりやすくなるので、マルチ・ピッキングに対応したピッキングカートや、倉庫管理システムを導入してミスを防止している企業が多くあります。
いずれにしろ、基本的な考え方なので、マルチ・ピッキング方式も含め、自社に適しているのはどの方式であるのか、比較検討しながら取組むことが大切です。
例えば、商品の出荷数が多い上位20%の商品で出荷ボリュームの大多数を占め出荷先が多いが、残りの商品は出荷先が限られている場合はどうするか?また、商品の入荷・在庫のタイミングと、出荷のタイミングが近い場合はどうするか?など、方式を組み合わせて考えるのも一つのやり方です。
※1.SKU
Stock Keeping Unitの略で受発注・在庫管理を行う時の、最小の管理単位。
商品の種類が多いアパレル商品で考えてみると、同じ商品であっても、色(白、青、赤、黄・・)やサイズ(S、M、L、XL・・)が複数あり得るので、同じ商品であっても、色・サイズの組合せで管理するため、商品点数も多くなります。
また、一般的には、次のような場合にSKUを区別するのがよいと言われています。
・商品名やブランド名が異なる場合
・価格、色、サイズ、包装状態、販売単位数量などが異なる場合
・100g入り、200g入りなど、商品の正味量が異なる場合
・セット商品で組合せや中身、価格が異なる場合
4.ピッキングの正確性・効率性を上げるには
では、自社に適うピッキング方式を選び、運用をするにあたり、より正確性・効果性を上げる方策を考えてみます。
(1)棚番管理(ロケーション)
例えば、工場をエリアに分けて、[エリア]-[列]-[段]-[間口]のようにルールを決めて棚番を付けることで、現場の整理整頓がしやすくなります。また、棚と棚の間の空間も、あまり狭くならないようにすることで、作業がスムーズになります。
(2)ABC分析
ABC分析とは、商品(在庫)を出荷頻度で3段階に評価する方法です。その結果を評価して、商品を置く棚番を変えることで、倉庫内での作業者の移動距離・時間を短縮することを目的とします。実際の運用に応じて3段階にこだわらず、ランクを考えて整理します。ただし、単純に適用するのではなく、置く棚を変える時に作業者に周知することも大切です。
「例」出荷頻度の実績を3段階に分け、出荷頻度に応じて商品を置く場所を変える。
・A商品…出荷頻度が高い商品
・B商品…出荷頻度が平均的な商品
・C商品…出荷頻度が低い商品
倉庫内棚配置《 変更前 》 《 変更後 》
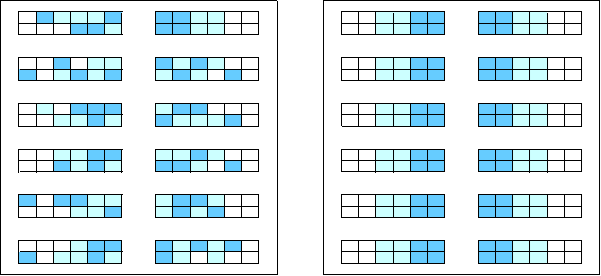
(3)ITツールの活用
倉庫内の作業員にとって、作業がしやすい環境を作ることも大切です。出荷指示書などの伝票に基づき、実際に商品を間違いなくピックアップし、梱包することに集中できることが、作業の効率化と正確性の向上につながります。
そのためには、ITツールを活用することに意義があります。自社のピッキング方式に適うソフトウェアやハードウェアを組み合わせて考えてみましょう。
例えば、ソフトウェアでは倉庫管理システムなどがあり、ハードウェアではHHT(※2)やスマートフォンなどを活用できます。
物流改善・在庫管理の課題解決「5つの事例」をご覧ください。どのような方法で改善し、どんな効果が得られたのかを解説しています。
※2.HHT
Handheld terminalsの略で、HT(Handy Terminal)と呼ばれることもある。
商品に付いているバーコード・QRコード・OCRなどを読み取って記録できる携帯端末のことを言います。
5.最後に
最初に考えたように、ピッキング作業自体は、比較的、単純な作業と考えられています。しかし、これまで考えてきたように、単純な作業であるからこそ、作業者の作業環境を良くすることが、出荷作業だけなく、顧客満足度の大きな違いにつながります。
作業環境の改善には、誤出荷、在庫差異、作業効率などのデータを取り、どこに課題があるのかを考え、対応を取った後も、継続的にデータを取り比較検討することが効果的です。その他、作業担当者の声も集めることも大切です。
おすすめコラム
おすすめ導入事例
課題解決に関する無料資料
お客さまの成功事例を事例集としてまとめました。以下のような資料を10本以上、無料配布中!
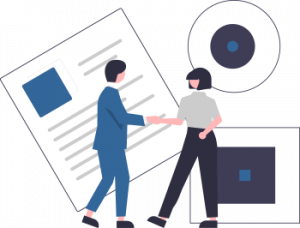
様々な課題解決事例集をご用意しています。
お気軽に資料請求ください。