働きやすい環境づくりを実現する、工程作業「見える化」の方法とは?
製造現場の意識改革に向け、タブレット活用で工場の見える化に成功した改善事例
公開日: 2022.11.24
HCSNewsLetter 第218号
取材協力
製造部 製造グループ グループ長
奥田 浩史 様
製造部 製造グループ チーム長
牛島 修一 様
ジャパンメディック株式会社様について
[所在地]
(本社)富山県富山市横越168番地
[事業概要]
医薬品、医薬部外品及び化粧品の製造販売
OTC外用剤(※)を製造販売するジャパンメディック様。従業員が働きやすい環境を目指し、現状把握・分析できる工程実績可視化システムを導入、現場改善の基盤づくりに成功した事例をご紹介します。
※OTC:薬局やドラッグストアなどで市販される医薬品
※外用剤:皮膚や粘膜に直接塗ったり貼ったりして使う薬
- 課題
- (1)工程のトラブル削減
(2)ライン稼働実績の把握
(3)改善意識の醸成
- 効果
- (1)トラブルの早期発見・対処が可能に
(2)正確な稼働実績の把握が可能に
(3)ライン稼働予実の対比が可能に
目次
働きやすい環境づくりを実現するための「3つの課題」
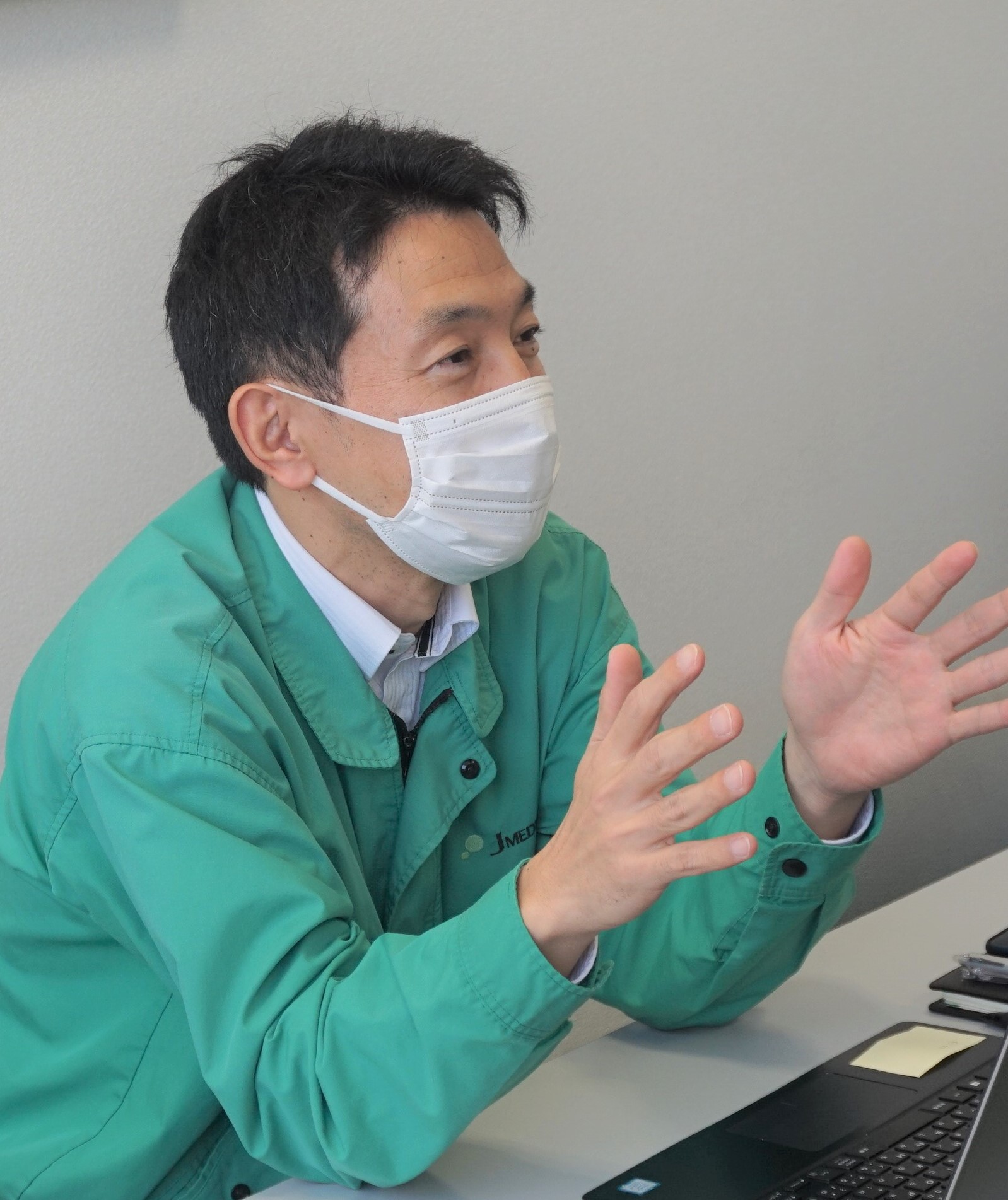
製造部 製造グループ グループ長 奥田 浩史 様
-検討のきっかけを教えてください-
当社で実施した従業員満足度調査がきっかけです。製造部の満足度が、他の部門に比べて低い結果になりました。「工程で発生するトラブルの対応が大変」「専門的な知識が得られない」と感じる作業者がいるようです。そこで、作業者が主体となって「働きやすい環境づくり」に取り組むことで、自身の成長や組織への貢献を実感し、少しでも仕事が楽しいと思ってもらいたい、と考えました。
-どのような課題をお持ちでしたか?-
課題1:工程のトラブル削減
作業者のモチベーション低下につながる、工程のトラブル削減を第一に考えました。トラブルが発生して、予定になかった残業や休日出勤が必要になると、従業員のメンタルに影響します。
特に最終工程である包装は、前工程のしわ寄せが多く、残業になってしまうケースが多いです。結果、包装チームの従業員満足度が一番低くなっています。担当者には子育て世代が多く、予定外の作業は負担が大きいと思います。
トラブルを減らそうとしたら、どれだけ減らすか目標設定が必要ですよね。でも、具体的な発生状況が分からず、目標が設定できなかったのです。まずは現状を知る必要がありました。
課題2:ライン稼働実績の把握
トラブルの発生状況を知るには、ラインの稼働実績をデータで記録し、把握する必要がありました。
充填ラインと包装ラインは一貫ラインであり、一方に作業遅延が生じると、もう一方にも影響が出ます。しかし以前の進捗管理方法は、現場の掲示板に1日2回手書きされる、各工程の「残りの所要時間」を見て把握するやり方。進捗に遅れがあっても、どの工程で何があったかは作業者に聞かないと分かりませんでした。また、本来ならば遅れの原因を明確にするべきですが、成り行きに任せていました。
原因の一つとなる製造過程のトラブルには、チョコ停のような小さなものから、品質に影響を与えるような大きなものまであります。大きなトラブルであれば、現場から責任者に報告があり、一緒に対応しています。でも、小さなトラブルは、現場で対処するケースがほとんどで、なかなか報告があがってきません。工程ごとの傾向を知りたくても、紙の製造日報を追いかける必要がありました。とてもじゃないですが追いきれません。
トラブルによるライン停止以外に、準備などの間接作業にどれだけ時間がかかっているか、遅延の原因になっていないか、を把握したいと思いました。
課題3:改善意識の醸成
作業者にやりがいを持ってもらうために、現状に満足せず、改善の意識を持ってもらいたいと考えました。
生産管理担当者が製造品目ごとに1週間の大まかな生産計画を立て、「だれが・何の製造品目を・どれだけ作るのか」を現場で計画しています。ただ、1日のスケジュールは、午前・午後といった大まかな時間割がホワイトボードで共有されるだけです。ラインをどれくらいの時間稼働させる予定なのかは、各作業者の頭の中にあるだけで共有されません。作業者には、本人が立てたライン稼働予定と実績のギャップを知り、問題意識を持ってもらいたいのです。そのためには予実を管理できるしくみが必要でした。
「3つの課題」を解決する「工程作業可視化システム」
-採用の決め手を教えてください-
当社の製造現場にマッチした、ライン稼働実績の収集方法をご提案いただいたことが決め手です。
以前参加したIoTイベントのブースで、HCSさんを知りました。「サイコロ」を使った実績収集システムの展示が印象的でしたね。6面を利用して工程のステータスを登録する方法に関心を持ち、HCSさんに相談しました。
最終的には、タブレット端末を使って実績を入力する方法にしましたが、QRコードやRFIDなど、いろいろな方法をご提案いただき、選択肢の豊富さに感心させられました。打合せを頻繁に実施して、当社の要望をくみ取っていただき、満足しています。
-工夫された点を教えてください-
Webシステムに各ラインの稼働予定と実績を登録して、PCやスマホでいつでも確認できるようにしました。
予定は、ライン毎に「準備」「生産」「休憩」「切替」などのステータス単位で時間割して、作業前日にPCを使って登録します。
実績は、各ラインでタブレット端末を使い、開始・終了時刻を登録します。各ステータスのボタンを押すだけでいいので、操作がとても簡単です。トラブルによるラインの異常停止も、同じようにボタンを押すだけで登録できます。タブレット端末は、充填ライン6か所と包装ライン6か所に配備しました。
また、最終工程の包装ライン6か所に、赤外線センサーを設置しました。完成品をカウントし、数量をPCでリアルタイムに確認できます。
導入効果・メリット
-取り組みの効果はいかがでしたか?-
効果1:トラブルの早期発見・対処が可能に
特に、チョコ停など、小さなトラブルの発生状況を見える化できた効果は大きいです。
「現場の判断で機械の微調整だけに留める→根本解決しないまま動かす→また停まる」を繰り返す状況が、放置されていることがありました。工程作業可視化システム導入によって、チョコ停を繰り返しているラインを発見でき、機械トラブルを根本解決するよう、設備担当に指示できるようになりました。
また、赤外線センサーでリアルタイムに完成品の数量を把握できるので、タブレットへの実績登録忘れがあったとしても、数量カウントの進み具合で異常を検知することもでき、助かっています。
効果2:正確な稼働実績の把握が可能に
現場に負担をかけない方法で、ライン毎の稼働実績を登録できるようになりました。タブレット端末でボタンをタップするだけなので、現場に運用が浸透するのは早かったです。
実績はすべてシステム上で管理されるので、日付やラインなどの検索条件で、すぐに実績を確認することができます。PCやスマホ・タブレット端末でいつでも状況が確認できるようになりました。
現場では「準備」「生産」の他「異常終了」「待機」のステータスを使い、ライン毎に実績を登録するので、どの工程で何が起きたのか、実績を細かく把握することができます。
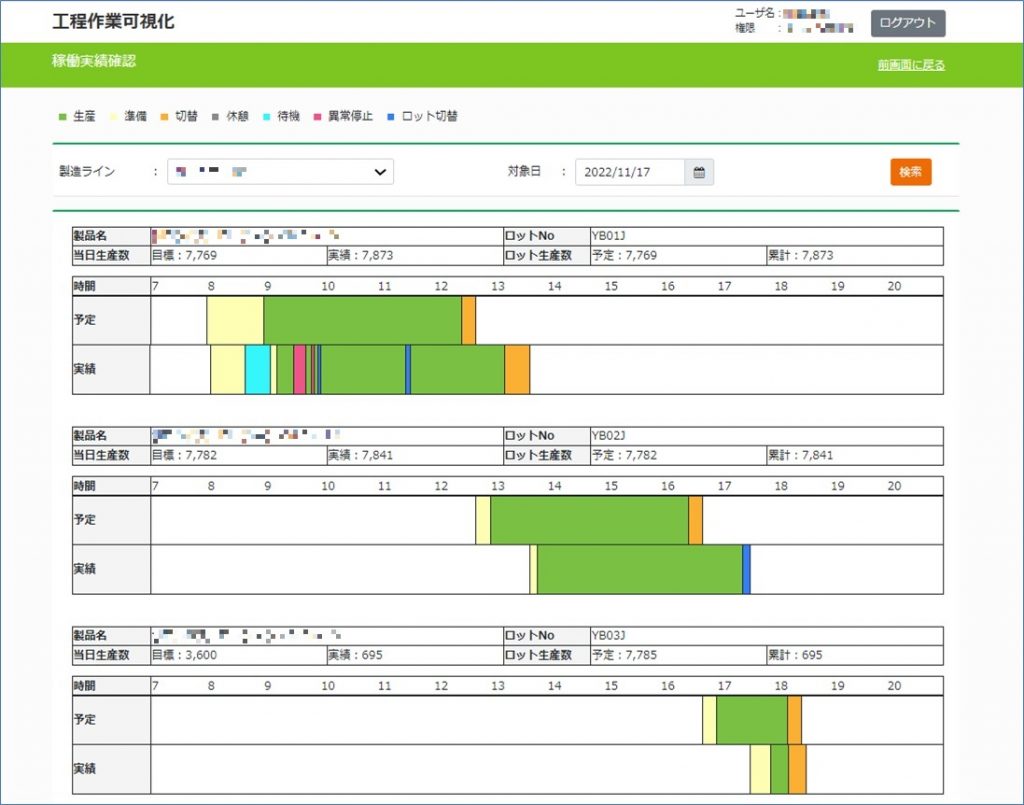
効果3:ライン稼働予実の対比が可能に
画面上では、作業者本人が登録した予定と実績が並べて表示されるので、比較しやすくなっています。現場の作業者からも「生産目標数量が見え、数値を意識して作業できるようになった」「生産実績を確認し、客観的な振り返りができるようになった」との声が挙がっています。直感的に予定と実績のギャップが把握できるので、改善に役立っています。ラインの稼働実績を基に、予定の精度を上げてほしいと思います。
今後の展望
-今後の展望を教えてください-
2022年度下期から、ライン停止率をグループの評価指標にしています。来年度からは作業者個人の評価指標にもしたいと思っています。個人に今期のライン稼働実績データ集計・分析から目標設定まで任せるつもりです。自分たちの力で現場を改善することで、作業しやすい環境を実現し、仕事にやりがいを感じてほしいですね。私たち責任者は改善の取り組みを支援したいと思います。
作業者には今の作業内容に満足せず、できることを増やしてほしいと思います。ラインの機械操作に加え、トラブル発生時のメンテナンスまで一通りこなせる人材が増えれば、ライン増加による人手不足の状況を改善できます。また、スキルがあがれば、作業者の評価はアップしますし、自身のモチベーション向上にもつながると思います。
作業者のモチベーション向上は、品質向上・お客様の満足度向上につながり、良い循環が生まれると思っています。
-インタビューにご協力いただきありがとうございました-
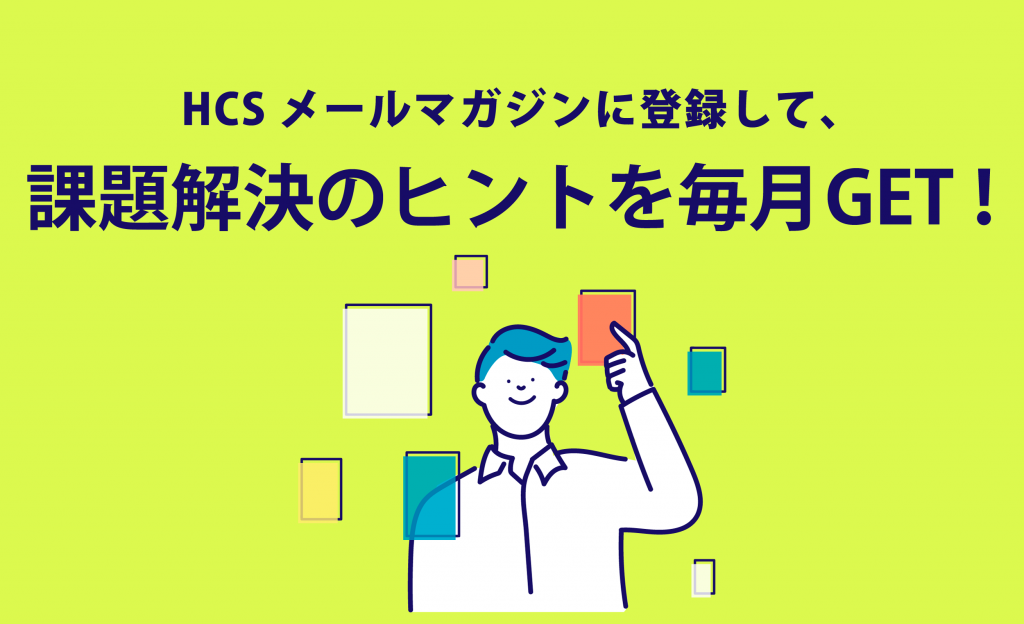
メルマガでお届け!北陸企業のIT活用事例から、課題解決のヒントが見つかる!!
(1)毎月、最新の事例をご紹介
(2)お客さまのIT活用成功事例を「事例集」として配信
(3)その他、コラムやイベント情報などをお知らせ
関連導入事例
製造業の課題解決「8の事例」
お客さまの成功事例を事例集としてまとめました。
製造業のペーパーレス化や業務効率化、生産性向上に成功した8の事例をご紹介。どのような方法で改善し、どんな効果が得られたのか?を解説しています。
工場内の状況をリアルタイムに把握する方法とは?
- 導入サービス:実績収集・見える化システム
- 課題
- (1)いつ何ができるのか把握したい
(2)誰が何をしているのか把握したい
(3)客観的根拠に基づき現場改善したい
- 効果
- (1)工程進捗がリアルタイムに確認可能
(2)作業者と作業時間の把握が可能
(3)実績データ蓄積による多角的な分析
月間 約4,000枚の図面や工程検査シートの削減に成功した方法とは?
- 導入サービス:TQ-Reporter
製造現場でタブレットの活用により、
(1)毎月約4,000枚の図面や工程検査シートのペーパーレス化に成功!
(2)簡単に書類を検索できるようになり、作業の効率がアップ!
(3)大量の印刷・ホッチキス留め・Excelへの転記作業がなくなり、時間を削減!
した事例をご紹介します。